De tous les métaux industriels utilisés pour les applications
structurales, le magnésium, d'aspect blanc et brillant, est celui qui
possède la plus faible densité. Elle représente les deux tiers de
l'aluminium (ou le quart de l'acier) tout en ayant des caractéristiques
mécaniques satisfaisantes.
Le magnésium est très malléable, ductile, mais peu tenace. On note une
faible valeur du module d'élasticité à la traction (172 GPa pour
l'aluminium), quelque soit son degré de pureté. Par contre, la résistance
à la traction atteint facilement 200 MPa, valeur assez élevée.
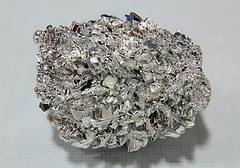
Inconvénient (corrosion) ou avantage (anode sacrificielle) selon les
utilisations, le magnésium possède un caractère chimique très marqué :
- pouvoir réducteur très puissant : potentiel électronégatif de -2.34 V,
- réactivité importante vis à vis des acides et de leurs sels.
Les alliages de magnésium peuvent globalement se grouper en deux familles
: ceux qui contiennent du zirconium, et ceux qui n'en contiennent pas. Cet
élément d'addition influe de manière prépondérante sur la structure
granulaire de l'alliage. Il permet d'obtenir une granulation très fine
(30~50 microns avec des moulages au sable) et relativement régulière si
l'on compare avec la structure dendritique des alliages Mg-Al-Zn.
Système magnésium - aluminium - zinc
La coulabilité de ces alliages permet de réaliser des pièces complexes
avec pratiquement tous les moulages connus. L'addition du zinc (Z) apporte
de bonnes caractéristiques mécaniques et améliore la coulabilité, mais
favorise la microporosité et les fissures à chaud, ce qui limite sa teneur
maximale à 3%. Lorsque c'est possible, on réalise un traitement thermique
qui permet d'augmenter la résistance à la rupture et la limite
d'élasticité.
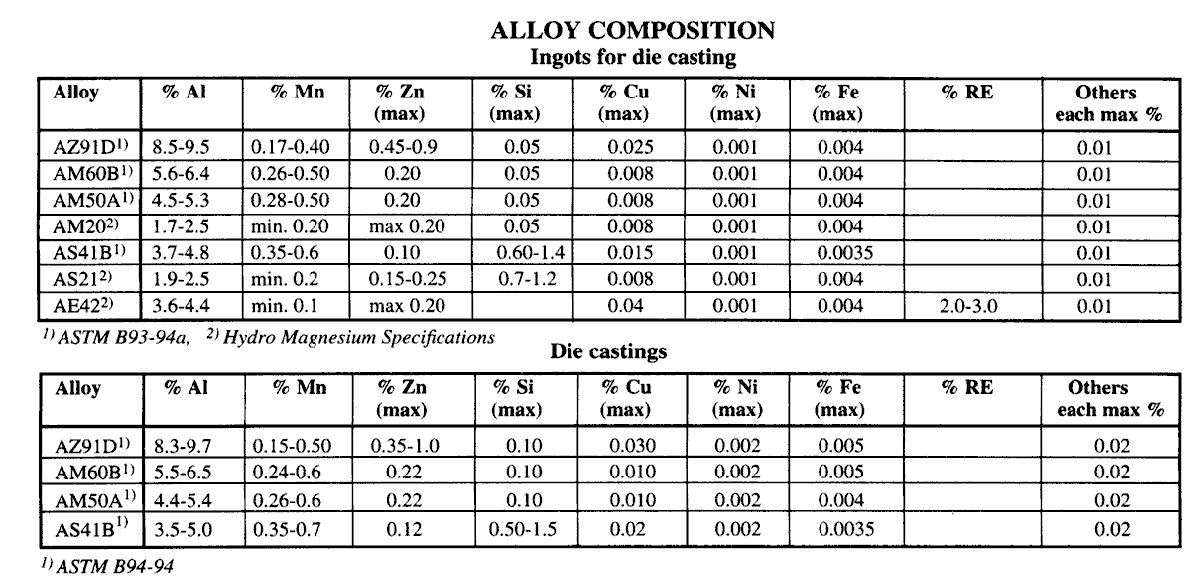
Traitement de surface
Le choix d'un traitement de protection dépend de l'environnement dans
lequel se situe la pièce : humidité et salinité de l'atmosphère,
confinement ou non de la pièce. On prête attention aux variations
possibles de l'ambiance comme dans le cas d'une pièce de moteur
alternativement en service et au repos, et donc alternativement sèche et
soumise à l'humidité ambiante. La fréquence des inspections, le coût de la
pièce, son accessibilité sont également des éléments importants à
considérer.
Les traitements envisageables se groupent en deux familles : les
traitements de passivation chimique (appelé aussi mordançage) et
électrochimique, et les revêtements. Par des essais comparatifs en
brouillard salin, on estime de manière approximative à 48 h
la tenue d'un mordançage acide, et à 96 h celle d'un mordançage neutre et
d'une oxydation anodique simple.
http://www.ardi-rhonealpes.fr/c/document_library/get_file?uuid=0fade6b2-479e-434e-875e-e8345f3a3ae8&groupId=10136