Le nickelage chimique (également appelé "sans courant" ou autocatalytique) est un procédé dans lequel un alliage de nickel est déposé par réduction des ions métalliques dans un bain dans lequel des sels de nickel sont dissous. La réaction de réduction est provoquée par l'ajout d'un agent réducteur chimique dans le bain (contrairement au nickelage électrolytique, où la réduction est provoquée par l'imposition d'un courant électrique). La température du bain est généralement de 90 °C, ce qui donne une vitesse de dépôt d'environ 20 µm/heure. À des températures plus basses, la vitesse de dépôt diminue. Les couches de nickel déposées avec cette technologie sont généralement des alliages Ni-P, mais les alliages Ni-B sont également possibles. Pour les applications industrielles, c'est le Ni-P qui est le plus utilisé. Les revêtements ont une dureté comprise entre 500 et 700HV, selon la quantité de phosphore ou de bore incorporée, mais peuvent être durcis à 900 - 1100HV par un traitement thermique approprié. Les revêtements de nickel chimique sont généralement moins résistants à l'usure que les revêtements de chrome dur, mais ils sont particulièrement résistants à la corrosion. En raison de la nature purement chimique du processus de dépôt, des pièces de formes complexes et de tailles diverses peuvent également être traitées avec une très grande uniformité de l'épaisseur du revêtement. Les revêtements de nickel chimique sont donc particulièrement adaptés aux applications sur des pièces de forme complexe où la résistance à la corrosion est le critère principal et la résistance à l'usure un facteur secondaire. Bien que les bains de nickelage soient moins toxiques que les bains de chromage, le nickelage nécessite la gestion d'effluents liquides toxiques car les bains doivent être remplacés régulièrement.

Bain pour le dépôt de nickel chimique En raison de l'absence de champ électrique,
l'épaisseur de la couche déposée dans le procédé sans courant est très uniforme.
Nature et propriétés des couches
Il existe plusieurs variétés de nickel chimique. Ils diffèrent principalement par le type d'agent réducteur utilisé dans le bain, qui détermine l'élément d'alliage inclus dans le dépôt (phosphore ou bore). La grande majorité des procédés de nickelage chimique utilisent des hypophosphites comme agents réducteurs, ce qui entraîne la formation d'un revêtement Ni-P. Selon la quantité de phosphore dans l'alliage, on distingue les couches à faible teneur en phosphore (1 à 4 %), à teneur moyenne en phosphore (5 à 8 %) et à forte teneur en phosphore (9 à 12 %). La teneur en phosphore détermine en partie les propriétés mécaniques et anticorrosion de la couche. Les alliages à faible teneur en phosphore sont les plus durs, mais avec une teneur en phosphore plus élevée, la résistance à la corrosion augmente.
Par un traitement thermique approprié, il est possible de former la phase intermétallique Ni3P qui augmente significativement la dureté. Après traitement thermique, les couches de Ni-P ont une dureté comprise entre 900 et 1100 HV. Le traitement thermique s'effectue à des températures comprises entre 300 et 400 °C.
Le tableau ci-dessous présente les propriétés des revêtements Ni-P chimiques.
Fonctionnalité
|
Valeur
|
Épaisseur de la couche
|
1 - 150 µm en général
Typiquement 15 - 50 µm
L'homogénéité de l'épaisseur, même sur des pièces complexes, est un grand avantage.
|
Dureté
après revêtement / après traitement thermique
|
Faible teneur en P : 650-750 / 1000- 1100 HV
Teneur moyenne en P : 550-700 / 1000-1100 HV
Haute teneur en P : 500-550 / 1000-1100 HV
|
Résistance à l'usure (indice d'usure Taber)
|
5-25 mg/1000 cycles
Les revêtements à faible teneur en phosphore ont une meilleure résistance à l'abrasion.
|
Coefficient de friction
(test du disque d'épingle avec une boule d'alumine)
|
0.4
|
Résistance à la corrosion
|
Faible teneur en P : moins bonne
Moyen P-contenu : bon
Teneur élevée en P : excellente
|
Qualité de la surface
|
Rugosité égale à celle du substrat pour les couches minces (jusqu'à 10-15 µm).
|
Température limite de fonctionnement
|
environ 320 °C
|
Outre les revêtements de NiP pur, des revêtements composites de NiP peuvent également être déposés en ajoutant au bain des particules submicroniques d'un autre matériau maintenu en dispersion. Les types les plus courants sont :
NiP-PTFE : l'incorporation de particules submicroniques de PTFE réduit le coefficient de friction et confère également au revêtement des propriétés anti-adhésives.
NiP-SiC et NiP-diamant : les particules dures de SiC ou de diamant augmentent la résistance à l'usure de la couche de NiP. Cependant, il faut noter que les particules dures peuvent provoquer une usure plus abrasive de la contre-face.
Applications
La résistance à l'usure des revêtements de nickel chimique est généralement légèrement inférieure à celle du chrome dur, mais meilleure que celle des revêtements de nickel électrolytique. Les revêtements NiP durcis sont utilisés comme alternative au chrome dur. Les revêtements de nickel chimique sont couramment utilisés lorsqu'un certain niveau de dureté de surface et de résistance à l'usure est requis en plus d'une bonne protection contre la corrosion. Les applications typiques sont les pompes, les rouleaux et les galets de pression, les vannes, les petits composants mécaniques, les filets de vis. Les revêtements NiP-PTFE sont utilisés dans les applications où un faible coefficient de frottement est requis, ou sur des composants tels que les vannes et les soupapes pour éviter le soudage à froid et la saisie. Les revêtements peuvent être appliqués sur une variété de matériaux de substrat : acier, acier inoxydable, cuivre et alliages de cuivre, alliages d'aluminium.
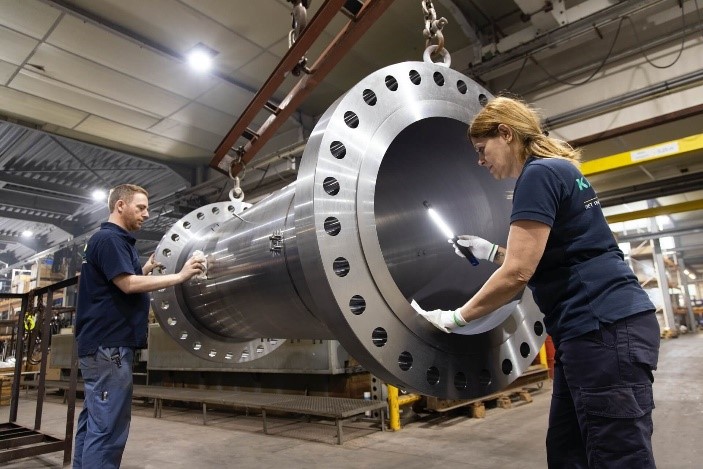
Traitement de petites pièces Application offshore

Protection d'une pièce avec filetage Couche de Ni-PTFE sur une plaque d'échantillonnage (secteur médical)
Protection contre l'usure et la corrosion par le nickel chimique dans diverses applications (https://www.kanigen.eu/en/home).
Comparaison entre le nickel chimique et le chrome dur
Dans la littérature anglophone, le nickel chimique est souvent appelé EN (= Electroless Nickel).
<Cr : inférieur au chromage dur actuel
=Cr : équivalent au chromage dur actuel
>Cr : meilleur que le chromage dur actuel
Critère
|
EN
|
EN après traitement thermique
|
Revêtements résistants à l'usure
|
X
|
<Cr
|
X
|
=Cr
|
Revêtements résistant à la corrosion
|
X
|
>Cr
|
X
|
=Cr
|
Grandes pièces
|
X
|
=Cr
|
X
|
=Cr
|
Très petites pièces
|
X
|
>Cr
|
X
|
>Cr
|
Pièces à géométrie complexe
|
X
|
>>Cr
|
X
|
>>Cr
|
Intérieur des cavités
|
X
|
>>Cr
|
X
|
>>Cr
|
Rechargement
|
X
|
<Cr
|
X
|
<Cr
|
Gestion des effluents
|
X
|
=Cr
|
X
|
=Cr
|
Respect de l'environnement et des opérateurs
|
X
|
>Cr
|
X
|
>Cr
|
Traitement des alliages thermosensibles
|
X
|
=Cr
|
X
|
<Cr
|
Processus économique (coûts énergétiques)
|
X
|
>Cr
|
X
|
=Cr
|
Robustesse
|
X
|
<Cr
|
X
|
<Cr
|
Productivité
|
X
|
<Cr
|
X
|
<Cr
|
Qualité de la surface après le dépôt
|
X
|
=Cr
|
X
|
=Cr
|