Dans la nitruration, l'azote (N) est introduit dans l'acier par diffusion pendant que la pièce est chauffée à 450 - 630 °C. Des temps de traitement longs, jusqu'à 100 heures, sont possibles. La couche nitrurée se compose de deux parties, appelées la couche blanche et la couche de diffusion. La figure 1 montre une coupe transversale d'un acier nitruré sur laquelle ces deux couches sont reconnaissables.
La couche blanche est une couche de nitrure de fer dure et inerte (nitrures Fe4N (γ') et Fe2-3(ε)) d'une épaisseur de 10 à 30 µm. Selon le type d'acier, la dureté est de 900 à 1500 HV.
La couche de diffusion a généralement une épaisseur de 100 à 200 µm, mais l'épaisseur peut atteindre 1 mm et plus dans les processus de nitruration à long terme. La couche de diffusion a une dureté plus élevée que la dureté du noyau en raison du durcissement par précipitation : ici, N se combine avec Fe et avec des éléments d'alliage tels que Cr, V, Ti, Al et Mo). La dureté de la couche de diffusion est également augmentée par l'azote dissous de manière interstitielle dans le réseau de ferrite. La dureté diminue du bord vers le cœur car la concentration de N diminue avec la profondeur. Typiquement, la dureté de la couche de diffusion est comprise entre 400 et 1000 HV.
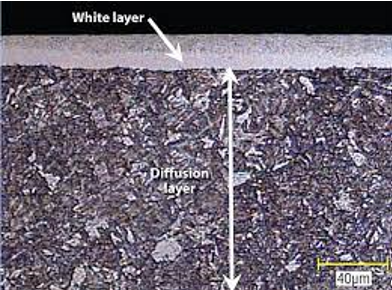
Figure 1 : Section transversale d'un acier nitruré. La couche blanche, constituée de nitrures de fer, est clairement visible. La zone située en dessous est appelée la couche de diffusion, qui se durcit par la précipitation de l'azote et par l'azote dissous.
On distingue les procédés de nitruration suivants :
- La nitruration gazeuse est le procédé le plus couramment utilisé. Le processus est réalisé dans un four rempli de NH3 (ammoniac) ou d'un mélange de NH3/H2/N2. La température est comprise entre 500 et 530 °C pour des durées de traitement de 10 à 120 heures. Une variété de matériaux et de pièces, de petite à très grande taille, y compris des formes complexes, peuvent être traités. Il existe différents types et tailles de fours.
- La nitruration en bain de sel est réalisée dans un bain de sels fondus (cyanures, cyanates). La température habituelle est d'environ 580 °C. On utilise des temps de traitement courts, de 1 à 3 heures, car des temps plus longs donnent une couche blanche trop épaisse et rugueuse. La rugosité et la porosité peuvent fortement augmenter en raison de l'attaque par le sel. La couche de diffusion (profondeur de nitration) est plutôt limitée. La nitruration en bain de sel est très adaptée au traitement en masse de petites pièces. En raison des substances toxiques contenues dans le bain de sel, le drainage et les déchets nécessitent un traitement spécifique.
- Dans la nitruration au plasma, la pièce est placée dans un four à vide. Le gaz est un mélange de N2, H2, CH4 et Ar à une pression de 2 à 6 mbar. Lorsque la pièce est mise sous haute tension négative à cette pression, un plasma s'enflamme, générant de l'azote atomique et des ions qui se diffusent plus facilement dans l'acier. La température habituelle est comprise entre 450 et 580 °C et les temps de traitement vont de 6 à 50 heures. Dans la plasmanitruration, la couche blanche est plutôt mince ou même absente. Dans ce dernier cas, le recuit au plasma peut être combiné au revêtement PVD dans le même four à vide.
Pratiquement tous les aciers, non alliés, faiblement alliés et fortement alliés, peuvent être nitrurés. La fonte est également nitrurée. Des duretés élevées peuvent être obtenues avec des aciers nitrurés qui contiennent des éléments d'alliage formant facilement des nitrures (Cr, Ti, Al, Mo, V). Par conséquent, les aciers à outils se prêtent bien à la nitruration. Les aciers inoxydables nécessitent un traitement spécifique lors de la nitruration pour ne pas perdre leur résistance à la corrosion.
En général, la nitruration et la nitrocarburation améliorent la résistance à la corrosion des aciers, mais dans une mesure limitée. Cependant, la résistance à la corrosion peut être considérablement améliorée par une post-oxydation. Dans ce procédé, après la nitruration, la pièce est exposée à une atmosphère oxydante à 350 - 400 °C, formant une couche d'oxyde de Fe de quelques µm d'épaisseur sur la couche blanche. Contrairement à l'acier, la couche d'oxyde de fer sur la couche blanche, qui est constituée de nitrures de fer, forme une couche fermée et bien adhérente, offrant une bonne protection contre la corrosion, même meilleure que le chrome dur.
Un processus connu impliquant une post-oxydation est le processus dit QPQ. Il s'agit de Quench/Polish/Quench, ce qui signifie qu'il faut suivre les étapes du processus : (bullet list)
- Nitrocarburation dans un bain de sels de cyanure fondus (Quench),
- Polissage, généralement dans un tambour vibrant (Polish),
- Post-oxydation en bain de sel (Quench).
La figure 2 montre que la protection contre la corrosion du procédé QPQ est supérieure à celle du chrome dur et même du nickel. Les noms commerciaux de ce procédé sont Tenifer, Tufftride, Melonite.
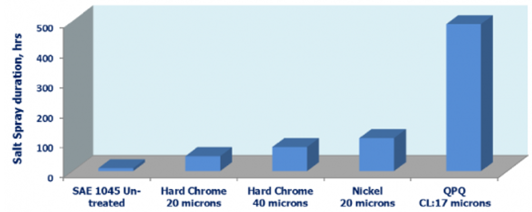
Figuur 2: Vergelijking van de corrosieweerstand van hardchroom, nikkel en QPQ-behandeling in een zoutneveltest (HEF USA).
Propriétés
Les propriétés les plus pertinentes conduisant à la nitruration et à la carbonitruration sont liées à la présence de la couche blanche (Fe-nitrures) et de la couche de diffusion (Précipitation et solution solide de N). La couche blanche dure et inerte signifie :
- Dureté de surface élevée, jusqu'à 1500 HV,
- Résistance élevée à l'usure, tant abrsasive qu'adhésive,
- Réduction du coefficient de frottement et amélioration des propriétés tribologiques dans les contacts mécaniques,
- Résistance améliorée à haute température,
- Résistance à la corrosion améliorée, en particulier lorsque la post-oxydation a été appliquée, la résistance à la corrosion est meilleure que celle du chrome dur.
La couche de diffusion signifie :
- Résistance élevée à la fatigue grâce à la présence de contraintes de compression,
- Augmentation de la capacité de charge.
La formation de nitrures entraîne une faible augmentation de volume. En théorie, cela permet également de modifier les dimensions d'une pièce, mais ces modifications sont très limitées. La température de la nitruration et de la carbonitruration est nettement inférieure à celle de la carbonitruration, ce qui signifie qu'il n'y a pas de risque de changement de taille ou de forme dû à des transformations de phase.
Applications
Les applications de la nitruration/carbonitruration sont multiples. Les composants mécaniques, grands et petits, sont traités pour réduire l'usure et augmenter la résistance à la fatigue :
- Engrenages, arbres et autres pièces des systèmes de transmission,
- Les composants des moteurs à combustion interne tels que les soupapes, les cames, les culbuteurs, les poussoirs, les axes.
- Diverses pièces de machines et composants hydrauliques.
Outils, aciers pour travail à froid et à chaud pour réduire l'usure par abrasion et par adhésion :
- Matrices, outils de formage, poinçons, matrices, lames pour le travail de la tôle,
- Matrices d'extrusion et matrices de coulée en acier.
Les composants de systèmes mécaniques tels que les mécanismes d'essuie-glace peuvent être fabriqués à partir de matériaux plus fins grâce à l'effet de renforcement de la nitrification.
Ressorts à gaz traités selon le processus QPQ
|
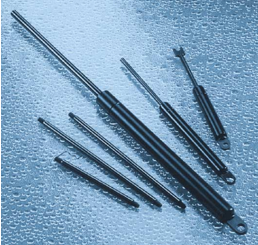
|
Diverses parties des voitures sont QPQ
traités contre l'usure et protection contre la corrosion.
|
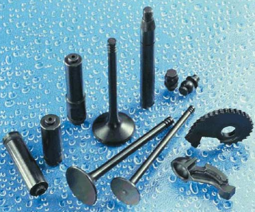
|
Buses nitrurées utilisées
dans la transformation des matières plastiques
|
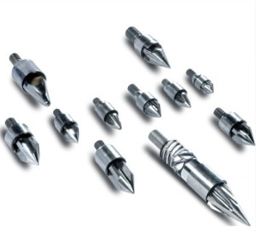
|
Plasmanitruration des engrenages |
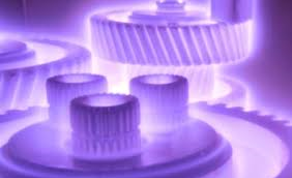
|
Moules pour parties du corps
des voitures sont nitrurées pour prolonger
prolonger leur durée de vie.
|
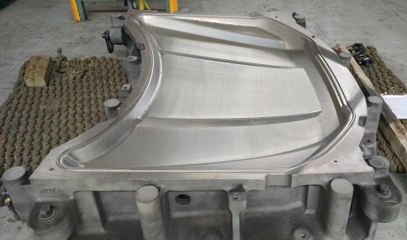 |