Le soudage à l'arc transféré par plasma est une technique dans laquelle un revêtement est formé sur un substrat par l'application de particules de poudre au cours d'un processus de soudage. Le revêtement déposé est dur et assez épais (plusieurs mm) et est lié métallurgiquement au substrat. La technique de soudage sur les revêtements est également appelée "hard facing". Grâce à l'ATP, les pièces usées peuvent être réparées ou les nouvelles pièces peuvent être rendues plus résistantes à l'usure et à la corrosion.
Le principe de la technologie PTA est expliqué plus en détail dans la section sur les procédés de traitement.
Les matériaux de départ utilisés pour former le revêtement soudé sur le substrat sont des poudres métalliques. Ils sont produits par atomisation à l'état fondu et ont une taille de particule comprise entre 40 et 150 µm. Les couches soudées peuvent être constituées de nombreux matériaux et combinaisons de matériaux différents, avec une large gamme de duretés et d'autres propriétés. Les principaux matériaux de substrat et de poudre sont les alliages suivants :
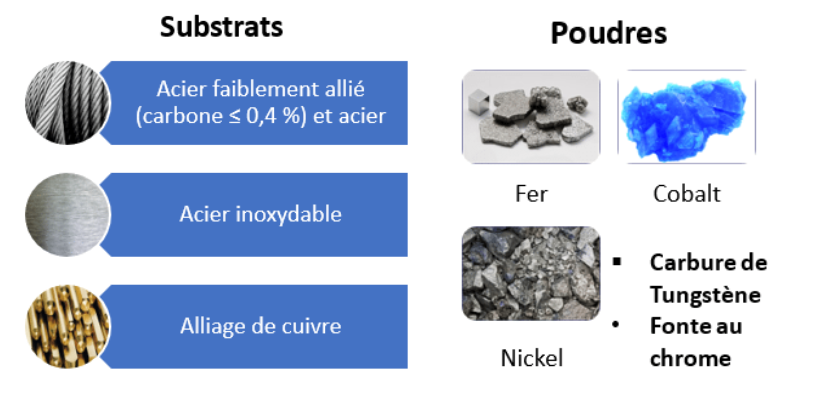
Les revêtements obtenus par PTA ont des propriétés très intéressantes :
- Une liaison métallurgique entre le revêtement et le substrat ;
- Une faible dilution (due au mélange avec le substrat) d'environ 5 à 15% ;
- Une zone à faible influence thermique ;
- Haute qualité du revêtement en termes d'homogénéité et de finesse de grain ;
- Taux de dépôt élevé et grande reproductibilité.
L'épaisseur du revêtement est de l'ordre du millimètre. En général, l'épaisseur peut varier de 1 à 4 mm, en fonction du matériau et des paramètres de dépôt. Plusieurs couches peuvent être appliquées l'une sur l'autre si nécessaire pour obtenir des couches épaisses supplémentaires. Pour une finition de surface optimale, un post-revêtement peut être nécessaire.
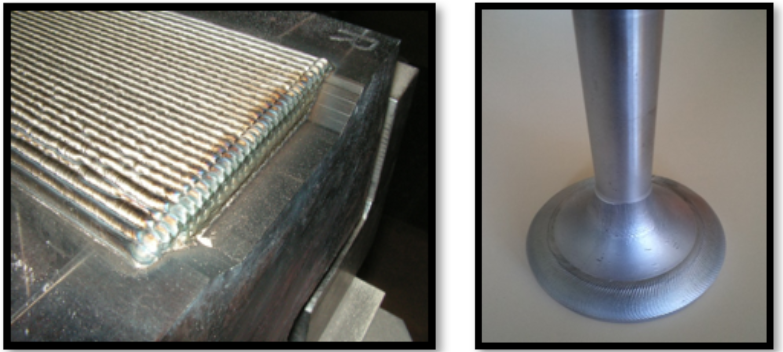
PERFORMANCE
Alliages de cobalt
Les alliages à base de cobalt, également appelés Stellite, sont constitués de Co avec des ajouts de Cr, C, W et/ou Mo. Ces alliages présentent les meilleures propriétés "globales" et combinent une excellente résistance à l'usure mécanique, notamment à haute température, avec une très bonne résistance à la corrosion. Ils sont généralement utilisés dans la plage de température de 315 à 600 °C. Les revêtements peuvent être refinis avec des finitions élevées, de sorte qu'ils ont un faible coefficient de friction qui donne de bonnes propriétés de glissement. Un exemple d'application est le revêtement des soupapes en acier des moteurs de voiture.
Alliages de nickel
Les alliages à base de nickel comportent généralement des ajouts de Cr, C, B, Fe et Si. Ils conservent leurs propriétés jusqu'à des températures d'environ 315°C et offrent également une bonne résistance à l'oxydation et à la corrosion. Ils couvrent une très large gamme de duretés : des alliages doux, tenaces et faciles à usiner aux alliages exceptionnellement durs et résistants à l'usure. Les alliages à faible dureté sont généralement utilisés pour les moules en verre. Les alliages à dureté élevée sont utilisés, par exemple, pour la reconstruction des lames des vis de transport, et ils peuvent être mélangés à des carbures pour obtenir un revêtement encore plus dur.
Alliages de fer
Les alliages à base de fer sont conçus pour résister à l'usure abrasive à basse température, généralement jusqu'à 200ºC. Par rapport aux alliages à base de cobalt et de nickel, leur résistance à la corrosion est également faible.
Cobalt |
+++ |
+++ |
++++ |
20 - 62 |
Nickel |
+++ |
++ |
++ |
20 - 62 |
+: Mauvais ; ++: Satisfaisant ; +++: Très bon ; ++++: Excellent.
CONTRAINTES INDUSTRIELLES
Le PTA est utilisé pour traiter des géométries assez simples : plates et peu courbes. Les petites et moyennes séries (50-100 pièces) sont les plus adaptées. Chaque partie est un cas en soi. Pour chaque combinaison de substrat et de revêtement, les paramètres optimaux doivent être déterminés en fonction de la géométrie et de la taille de la pièce. Naturellement, la commande du robot doit également être adaptée à la pièce. Il est recommandé de nettoyer la surface du substrat et d'éliminer les couches d'oxyde avant d'appliquer le revêtement. En particulier dans le cas des aciers fortement alliés, le substrat doit être préchauffé et maintenu chaud (conservé dans de la vermiculite) pour éviter la fissuration et la formation d'une structure très dure dans la zone d'influence thermique.