PVD (Physical Vapour Deposition) est un nom général pour plusieurs procédés de dépôt sous vide. Une caractéristique du PVD est que le processus commence avec le matériau de revêtement en phase solide, puis le matériau de revêtement passe en phase vapeur, et les vapeurs précipitent et se condensent sur le substrat de sorte qu'une couche mince est déposée. Pour que ce processus soit efficace, il doit se dérouler dans une chambre à vide. La chambre est d'abord pompée jusqu'à une pression inférieure à 10-5 mbar, puis de l'argon est fourni comme gaz de traitement à une pression d'environ 10-3 mbar. L'introduction du matériau de revêtement dans la phase vapeur peut se faire de la manière suivante :
- Dans l'évaporation thermique, le matériau de revêtement est contenu dans un creuset et s'évapore par chauffage. Ce procédé est principalement appliqué pour vaporiser des films d'aluminium, par exemple comme revêtement miroir, comme revêtement barrière sur les films d'emballage ou comme couche thermoréfléchissante sur les matériaux d'isolation.
- Dépôt assisté par ions : dans ce procédé, un plasma est allumé dans le gaz de procédé Ar et le substrat est porté à une haute tension négative. Par conséquent, la couche est bombardée d'ions pendant le processus de dépôt, ce qui assure une meilleure adhérence et une plus grande densité (moins de porosités) de la couche. Si un gaz réactif est également fourni (voir ci-dessous), le plasma facilite la réaction avec le gaz réactif.
- Dans le procédé de pulvérisation, le matériau de revêtement se présente sous la forme d'une plaque plane. Cette plaque se trouve dans un champ magnétique et est portée à une haute tension négative de sorte qu'un plasma intense se forme juste au-dessus de la plaque. Les ions tombent avec une énergie élevée de sorte que le transfert de momentum entraîne la pulvérisation d'atomes loin du matériau de revêtement et dans la phase vapeur. Les atomes pulvérisés ont une énergie élevée, bien supérieure à l'énergie thermique, et les revêtements déposés par pulvérisation sont donc de meilleure qualité que les revêtements évaporés. Le champ magnétique provient d'aimants permanents disposés derrière la plaque plane et le procédé est également appelé pulvérisation magnétron. La figure 1 montre une représentation schématique d'un procédé de pulvérisation magnétron.
- Dans l'évaporation par arc, un arc électrique est généré entre le matériau de revêtement, qui est en forme de disque, et une électrode située au-dessus du disque. Au point où l'arc touche le matériau de revêtement, ce dernier s'évapore. Une caractéristique de cette évaporation est qu'une partie importante de la vapeur est ionisée. Ces ions sont accélérés dans un champ électrique et frappent donc le revêtement en croissance avec une énergie élevée. De cette manière, l'évaporation à l'arc permet d'obtenir des revêtements denses et bien adhésifs.
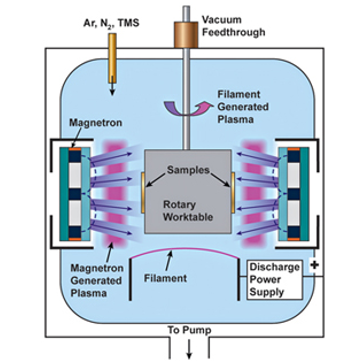
Figure 1 : Représentation schématique d'un procédé de pulvérisation magnétron dans une configuration
typique des équipements de dépôt industriels.
Dans tous ces procédés PVD, le matériau de revêtement est généralement un métal pur et un ou plusieurs gaz réactifs sont introduits pendant le processus de dépôt pour créer des composés tels que des revêtements céramiques. Les gaz réactifs utilisés sont N2 pour obtenir des nitrures métalliques, C2H2 pour les carbures métalliques, et O2 pour les oxydes. La réactivité du gaz est accrue par le plasma présent dans la plupart des procédés. De cette façon, les revêtements céramiques PVD typiques tels que TiN, TiCN, CrN, TiAlN sont déposés.
En principe, les revêtements peuvent être appliqués à température ambiante, mais la plupart du temps, la température est augmentée car cela a un effet positif sur la qualité des revêtements. En pratique, les températures de dépôt varient entre environ 200 °C et 500 °C, en fonction de la charge thermique maximale du substrat.
Le procédé PVD est un procédé en ligne de visée car, en raison de la faible pression dans la chambre de dépôt, les particules de vapeur ne subissent pas de collisions avec les molécules de gaz présentes (gaz de procédé et gaz réactif) et se déplacent donc en ligne droite de la source au substrat. Les substrats non plats doivent subir des mouvements de rotation pour être recouverts d'une couche de revêtement uniforme et les trous ou cavités profondes sont difficiles à revêtir. Le taux de déposition est de 1 à quelques µm par heure.
Pour obtenir une bonne adhésion, la surface du substrat doit être très propre. Outre le nettoyage et le dégraissage classiques, l'étape finale de nettoyage de précision a lieu dans la chambre à vide et constitue en fait la première étape du processus de dépôt. En allumant un plasma, la surface du substrat peut être attaquée par bombardement ionique, éliminant ainsi les dernières impuretés.
Propriétés des revêtements PVD
Les épaisseurs courantes des revêtements PVD sont comprises entre 1 et 10 µm et généralement entre 2 et 5 µm. La figure 2 montre une vue en coupe d'un revêtement TiN. On voit clairement la microstructure colonnaire qui est une caractéristique typique des revêtements PVD. Cette structure s'accompagne également de la présence de pores. Les revêtements PVD peuvent également contenir des défauts de type "pinhole", qui sont la conséquence des fortes contraintes de compression dans la couche. Outre la lenteur de la déposition, les contraintes internes élevées font que l'épaisseur de la couche est limitée. La surface des revêtements PVD reproduit la surface du substrat.
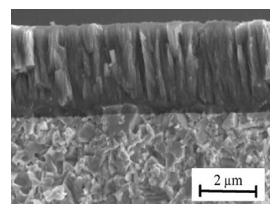
Figure 2 : Vue en coupe d'un revêtement PVD TiN.
Le tableau ci-dessous donne les propriétés de certains revêtements PVD couramment utilisés.
Coating
|
TiN
|
TiCN
|
TiCrN
|
CrN
|
AlCrN
|
AlTiN
|
AlTiCrN
|
WC/C
|
Hardness
HV
|
2500
|
2800
|
2200
|
2300
|
3000
|
3500
|
3200
|
1500
|
Friction Coeff. to steel
|
0,55
|
0,3
|
0,55
|
0,55
|
0,55
|
0,55
|
0,55
|
0,1
|
Max. Temp. Of Use °C
|
500
|
300
|
500
|
700
|
1000
|
700
|
850
|
250
|
Les revêtements PVD ont une dureté très élevée, allant de 1500 HV à 3500 HV et même plus. La dureté dépend du type de revêtement PVD et des contraintes internes. Ils présentent un coefficient de frottement inférieur à celui de l'acier et, en raison de leur nature céramique, ils réduisent l'usure des adhésifs. Par conséquent, les revêtements PVD ont une très grande résistance à l'usure et la protection contre l'abrasion est la principale raison de leur utilisation. Une mise en garde s'impose : les revêtements PVD sont fins et moins adaptés à la protection contre les charges ponctuelles. Par conséquent, ils sont généralement utilisés sur les aciers trempés. En principe, les revêtements PVD peuvent être déposés sur tous les métaux, mais pour les matériaux plus tendres comme l'aluminium, il est recommandé d'appliquer d'abord une couche de nickel.
Le revêtement WC/C a des propriétés différentes de celles des autres revêtements (voir tableau). Ce revêtement est déposé par pulvérisation de carbure de tungstène (WC) avec du C2H2 comme gaz réactif. En raison de l'incorporation de C (et H) supplémentaires, le revêtement est moins dur et acquiert un coefficient de friction très faible. Par conséquent, ce revêtement est largement utilisé dans les contacts tribologiques.
La protection des revêtements PVD contre la corrosion est limitée. Cela est dû au fait qu'ils sont minces, que la microstructure n'est pas 100% dense, et principalement à cause des trous d'épingle. Certains revêtements PVD tels que le CrN présentent des contraintes internes plus faibles, peuvent être appliqués plus épais et protègent légèrement mieux contre la corrosion. Il est également possible d'appliquer des structures multicouches qui présentent moins de défauts de trous d'épingle et offrent une meilleure protection contre la corrosion, mais la protection contre la corrosion n'est pas l'objectif principal des revêtements PVD.
Applications
Les revêtements PVD sont bien connus pour leurs applications sur les outils (aciers trempés laminés à froid et à chaud) et les composants mécaniques :
- Outils d'usinage tels que forets, fraises, fraises à dessiner, plaques de coupe ;
- Poinçons, matrices, couteaux pour la transformation des métaux et des matières plastiques
- Outils de transformation et matrices de formage pour le traitement de la tôle ;
- Filières d'extrusion et moules d'injection dans la transformation des matières plastiques ;
- Matrices d'extrusion et matrices pour le moulage à haute pression dans le traitement de l'aluminium.
- Composants mécaniques : il s'agit de petites pièces mécaniques telles que les pièces mobiles des moules, les pièces des moteurs et des pompes, les pièces de machines. Dans de nombreux cas, un revêtement à faible friction tel que le revêtement WC/C est utilisé ici.
Les revêtements PVD peuvent non seulement prolonger la durée de vie des outils d'un facteur de 10 à 100, mais ils ont également un effet sur la qualité du produit.
Outils d'usinage revêtus d'AlCrN
|
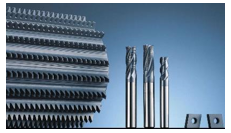
|
Outils de transformation pour l'acier à haute résistance revêtu d'AlTiN
|
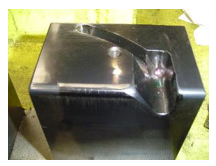
|
Matrice de colonne pour tôles d'acier galvanisé revêtues de WC/C
|
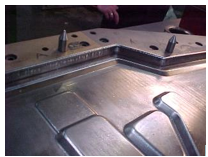
|
Moule d'extrusion pour tuyaux en plastique revêtus de CrN (Oerlikon Balzers)
|
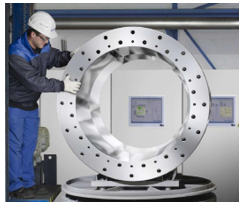
|
Pièces mécaniques revêtues de WC/C
|
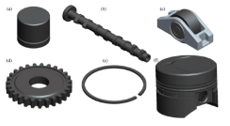
|