La figure montre le principe de fonctionnement du rechargement au
laser. Le faisceau laser se déplace sur la surface et crée un bain de fusion. Le rechargement dur (laser cladding en anglais) est utilisé pour améliorer les propriétés du matériau de base, principalement la résistance à l'usure et à la corrosion. Ce procédé constitue donc une alternative aux revêtements de chrome dur.
Une caractéristique essentielle des revêtements soudés est qu'ils sont liés métallurgiquement au substrat, ce qui confère aux couches une très grande résistance aux chocs et une bonne protection contre la sous-corrosion. Les paramètres importants sont l'apport de chaleur, la zone affectée par la chaleur et le mélange (dilution) du revêtement et du substrat.
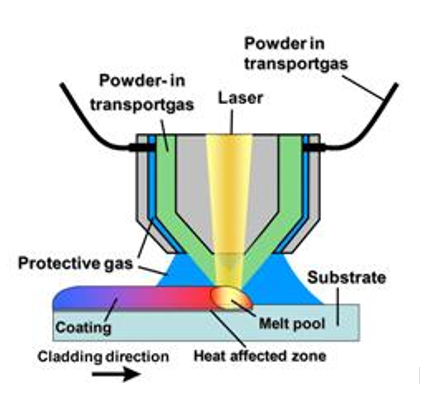
La figure montre le principe de fonctionnement du gainage laser. Le faisceau laser se déplace sur la surface et crée un bain de fusion. En même temps, les particules de poudre sont acheminées vers la surface par un gaz porteur, fondent dans le faisceau laser et forment le revêtement, qui est partiellement mélangé au substrat fondu. Le revêtement est appliqué localement et le masquage n'est donc pas nécessaire. Les cordons de soudure ont une largeur de 1 à 5 mm et l'épaisseur de la couche est comprise entre 0,2 et 1 mm. Des couches plus épaisses peuvent être constituées par des passages multiples du laser. Un post-traitement est nécessaire pour obtenir une surface lisse. L'une des possibilités est la refonte au laser, qui permet d'obtenir un meilleur état de surface. Dans le processus ordinaire de rechargement par laser, la tête du laser se déplace à une vitesse de 2 m/min. Récemment, des procédés à (ultra) grande vitesse ont été développés, permettant d'atteindre des vitesses allant jusqu'à 150 m/min. À ces vitesses élevées, l'épaisseur des revêtements est plus faible, à savoir 0,1 - 0,3 mm, et les cordons de soudure sont plus étroits, ce qui donne une surface dont la rugosité est fortement réduite (typiquement 5 µm Ra). Dans le gainage laser, l'apport de chaleur, la zone affectée par la chaleur et le mélange sont réduits au minimum par rapport aux autres techniques de gainage. Cela permet d'obtenir une grande qualité de revêtement.
Les poudres utilisées déterminent les propriétés de la couche et la dureté, la résistance à l'usure, la ténacité et la résistance à la corrosion peuvent être modifiées en fonction du type de poudre. Les poudres utilisées sont les mêmes que pour le soudage par recouvrement PTA et de nombreux types sont disponibles :
Co-alliages : résistance à l'usure et à la corrosion jusqu'à haute température,
Alliages de nickel : résistance à l'usure et à la corrosion,
Alliages de fer : solidité, ténacité, résistance à l'usure (abrasion et érosion).
Des poudres composites métal/céramique telles que Co-WC ou Ni-WC peuvent également être utilisées, augmentant encore la dureté et la résistance à l'usure. La vitesse de solidification élevée permet d'obtenir une microstructure fine et empêche les carbures de se dissoudre dans la matrice métallique. Cela contribue à la dureté et à la qualité des revêtements.
Le tableau ci-dessous compare les propriétés des revêtements déposés par PTA, par rechargement au laser et par projection thermique. Ces trois méthodes permettent d'appliquer des revêtements épais (jusqu'à plusieurs millimètres). Les revêtements épais sont indiqués dans des conditions hautement abrasives.
Fonctionnalités |
PTA
|
Rechargement au laser
|
Projection thermique
|
Mélange
|
5-60 %
|
5-10 %
|
Non
|
Apport de chaleur
|
Elevé |
Bas
|
Bas
|
Adhésion
|
Métallurgique
|
Métallurgique
|
Mécanique
|
Porosité
|
Non
|
Non
|
0,5-20 %
|
Épaisseur du substrat
|
> 5 mm
|
> 1 mm
|
> 0,5 mm
|
Épaisseur de la couche
|
1 – 10 mm
|
0,1 – 2 mm
|
0,1 – 2 mm
|
Résistance à l'usure
|
Elevé
|
Elevé
|
Très élevé
|
Résistance aux chocs
|
Elevé
|
Elevé
|
Bas |
Résistance à la corrosion
|
Elevé
|
Elevé
|
Moyen
|
Mise en oeuvre
Le rechargement par laser convient parfaitement au traitement de composants à géométrie axiale ou conique. Dans ce cas, le composant tourne et la tête laser peut se déplacer en parallèle selon la direction de l'axe. Le traitement de surfaces plus complexes est également possible, ce qui nécessite un processus robotisé. Les surfaces à traiter doivent être accessibles par la tête du laser. Le traitement de l'intérieur des angles n'est donc pas totalement possible. Le traitement interne des tuyaux est toutefois possible à partir d'un diamètre d'environ 50 mm. Les surfaces doivent être propres et exemptes de corrosion. Dans certains cas, selon le type de matériau du substrat, un préchauffage peut être nécessaire. Le rechargement au laser est une technique peu polluante. Le seul déchet est la poudre, qui peut être recyclée. Les grands composants difficiles à transporter peuvent être traités sur place.
Le revêtement au laser est utilisé à la fois pour appliquer des couches protectrices et pour effectuer des réparations localisées sur une surface. La plupart des applications se situent dans l'industrie lourde :
- Industrie pétrochimique
- Industrie nucléaire
- Moteurs à turbine
- Transports (chemins de fer, camions, automobiles)
- Machines agricoles
Cette technique se prête également à l'accumulation de matériau couche par couche, comme la formation des dents d'une roue dentée, et peut donc être considérée comme une technique de "fabrication additive".
Application d'un revêtement de protection contre la corrosion et l'usure
|
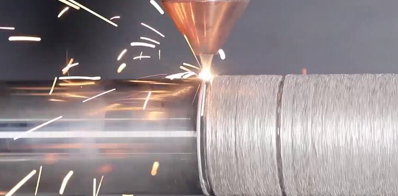
|
Réparation locale
|
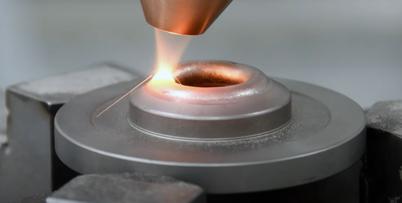
|
Construction de dents d'un engrenage
(Source Vito)
|
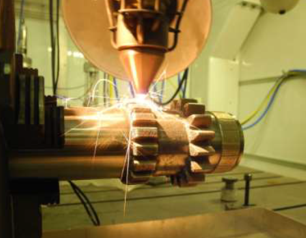
|