Dans le processus de projection thermique, les particules fournies d'une poudre ou d'un fil sont fondues dans la buse, puis projetées à grande vitesse sur le substrat avec de l'air comprimé. Ce principe est illustré dans la figure 1. Lorsque les particules fondues atterrissent sur le substrat, elles se solidifient rapidement pour former le revêtement. Les particules se déplacent de manière rectiligne, ce qui signifie que le processus est un processus de dépôt en ligne de mire. Cela signifie que la projection thermique est plus susceptible d'être limitée aux pièces à géométrie non complexe.
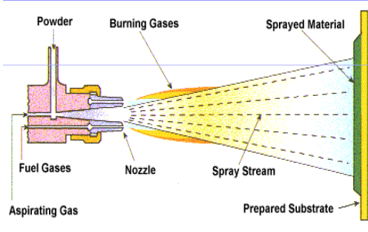
Figure 1 : Principe des procédés de projection thermique.
La figure 2 montre schématiquement la structure d'un revêtement projeté thermiquement. L'adhésion des revêtements se fait principalement par ancrage mécanique. Par conséquent, la surface du substrat doit être suffisamment rugueuse pour obtenir une adhérence suffisante. Les revêtements peuvent contenir des défauts tels que des pores, des particules non fondues et des inclusions d'oxydes. La surface du revêtement présente une certaine rugosité et un post-traitement est nécessaire pour obtenir une surface lisse. La projection thermique permet d'appliquer des couches épaisses, généralement de l'ordre de 0,1 à 2 mm.
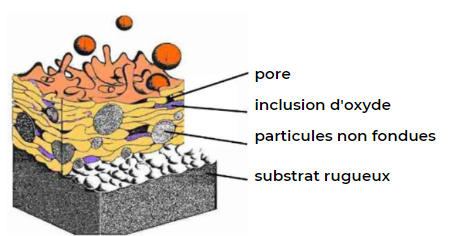
Figure 2 : Représentation schématique de la structure d'une couche projetée thermiquement.
Habituellement, les revêtements sont des revêtements composites métal/métal du type métal/carbure métallique ou métal/oxyde métallique, mais bien sûr, des revêtements purement métalliques et même des revêtements purement céramiques (par projection de plasma) peuvent également être appliqués. En principe, le revêtement peut être appliqué à de faibles températures du substrat, ce qui signifie que non seulement l'acier, mais aussi les alliages d'aluminium ou de cuivre peuvent être traités par projection thermique. Dans de nombreux cas, le substrat est préchauffé, ce qui permet une meilleure adhésion car les particules fondues se solidifient alors moins vite.
- La projection thermique comporte un certain nombre de variantes qui dépendent de la manière dont les particules sont fondues dans la buse.
- La projection autogène ou projection à la flamme : elle utilise la chaleur d'une flamme d'oxygène et d'acétylène pour faire fondre les particules fournies. Ce procédé est principalement utilisé pour appliquer des revêtements métalliques tels que les alliages Zn-Al pour la protection contre la corrosion, mais il peut également être utilisé pour appliquer des revêtements composites métalliques.
- La projection à l'arc électrique : un arc est tiré entre deux électrodes pour faire fondre les particules de poudre ou le fil d'alimentation.
- La projection à plasma : ici, un plasma est allumé dans un gaz porteur qui est un mélange d'argon, d'hélium, d'azote et d'hydrogène. Le plasma permet d'atteindre des températures très élevées, jusqu'à 20 000 °C, ce qui permet également de faire fondre des poudres céramiques pures et de les appliquer comme revêtements.
- Le plasma permet d'atteindre des températures très élevées, jusqu'à 20 000 °C, ce qui permet également de faire fondre des poudres céramiques pures et de les appliquer comme revêtements.
- Procédé HVOF : HVOF signifie "High Velocity Oxygen Fuel" (combustible oxygéné à haute vitesse). La caractéristique de ce procédé est la vitesse supersonique (jusqu'à 700 m/s) à laquelle les particules fondues sont projetées sur le substrat. En raison de la vitesse élevée, la qualité des revêtements HVOF est nettement meilleure, ce qui se manifeste par une meilleure adhérence et moins de porosités dans le revêtement. Par conséquent, le procédé HVOF est le procédé standard pour appliquer des revêtements anti-usure.
- La projection à gaz froid : dans ce procédé de projection, les particules de poudre sont projetées sur le substrat à des vitesses supersoniques pouvant atteindre 1200 m/s sans que les particules ne fondent. En raison de leur énergie cinétique élevée, ils sont déformés plastiquement lors de l'impact et adhèrent donc à la surface du substrat ou du revêtement. Ce procédé ne convient qu'aux matériaux qui sont plastiquement déformables, comme les métaux et les alliages.
Dans le tableau ci-dessous, les propriétés des revêtements déposés par les différents procédés sont données et comparées.
Property
|
Wire Flame spraying
|
Powder Flame spraying
|
Arc spraying (ARC)
|
Plasma spraying
(APS)
|
HVOF spraying
|
Cold spraying
|
Tpowder(°C)
|
<3000
|
<3000
|
<5000
|
<16000
|
<3000
|
<800
|
Tsubstrate(°C)
|
50 -150
|
100-150
|
50-125
|
100-125
|
100-125
|
22-120
|
Speed (m/s)
|
150-240
|
25-35
|
150-400
|
300-500
|
800-1200
|
400-1500
|
Coating materials
|
Metals, Alloys, M/MC
|
Metals, Alloys, M/MC,
Polymers
|
Metals, Alloys, M/MC
|
Metals, Alloys, M/MC
Ceramic
|
Metals, Alloys, M/MC
|
Metals, Alloys
|
Deposition rate (kg/h)
|
2,5 - 30
|
3 - 9 metal. 1,5-2,5kera.
|
4,5 - 55
|
3 - 9
|
4 - 5
|
0,3 - 3
|
Adhesion (MPa)
|
6 - 10
|
6 – 10
|
10 – 20
|
20 – 70
|
>70
|
30 - 35
|
Relative cost (1=low, 6=high)
|
3
|
3
|
1
|
5
|
5
|
6
|
La dureté et la résistance à la corrosion du revêtement projeté thermiquement sont déterminées par les propriétés du matériau de revêtement lui-même. Pour les applications anti-usure, les revêtements métalliques composites à base de carbure de tungstène et/ou de carbure de chrome avec Co ou Ni sont le plus souvent appliqués par le procédé HVOF. Ce sont également ces types de revêtements qui constituent des alternatives aux revêtements en chrome dur. Ces revêtements offrent également une bonne protection contre la corrosion.
La figure 3 donne un aperçu des types de revêtements possibles par les procédés de projection thermique.
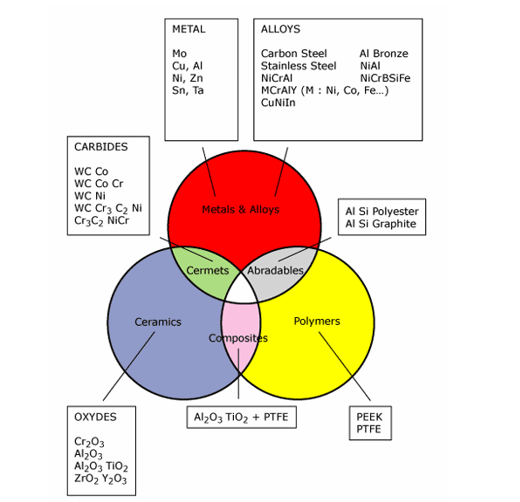
Figure 3 : Aperçu des types de revêtements appliqués par projection thermique.
La projection thermique ne convient pas au traitement en masse de petites pièces. Les pièces à traiter sont traitées pièce par pièce. L'application locale du revêtement est possible. Comme ce procédé implique une certaine contrainte thermique sur le substrat, il ne convient pas non plus aux pièces très petites et très fines. Les applications typiques des revêtements appliqués par projection thermique sont :
- Gros roulements utilisés dans les trains d'atterrissage
- Essieux
- Tiges de piston hydrauliques telles qu'utilisées dans les applications offshore (protection contre l'usure et la corrosion)
- Rouleaux utilisés dans les industries de l'acier, du verre et du papier.
- Composants de machines, par exemple dans l'industrie textile
- Vannes d'arrêt, vannes à bille
- Dans le secteur médical, le revêtement par projection thermique est utilisé sur des implants tels que les articulations artificielles.
- Les réparations et les corrections de taille sont également possibles grâce à des revêtements appliqués par projection thermique.
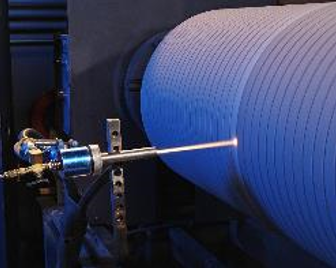