Les dépôts chimiques de nickel-bore résultent de la réduction de sels de nickel par l’oxydation d’un agent réducteur, en général, le borohydrure de sodium (NaBH4). En plus de la source de nickel et de l’agent réducteur, un agent complexant, un stabilisant et un régulateur de pH sont utilisés dans le bain de revêtement de nickel-bore. Cette technique présente beaucoup d’avantages : production de revêtements uniforme même sur les substrats de formes complexes, possibilité de revêtir des substrats non-conducteurs, propriétés intéressantes telles qu’une dureté élevée, une excellente résistance à l’abrasion. Cette technique ne nécessite pas de moyens onéreux pour sa mise en œuvre. Pour ces raisons, cette technique est utilisée dans plusieurs secteurs pour des applications diverses.
En général, les stabilisants utilisés pour cette technique sont toxiques (ex : les sels de plomb), néanmoins, le dépôt étudié dans le cadre du projet d’ALTCTRLTRANS est produit dans un bain qui ne contient pas de stabilisant toxique.
NATURE DES COUCHES ET PROPRIETES
Les
propriétés du dépôt développé dans le cadre de ce projet sont présentées dans le
tableau ci-dessous :
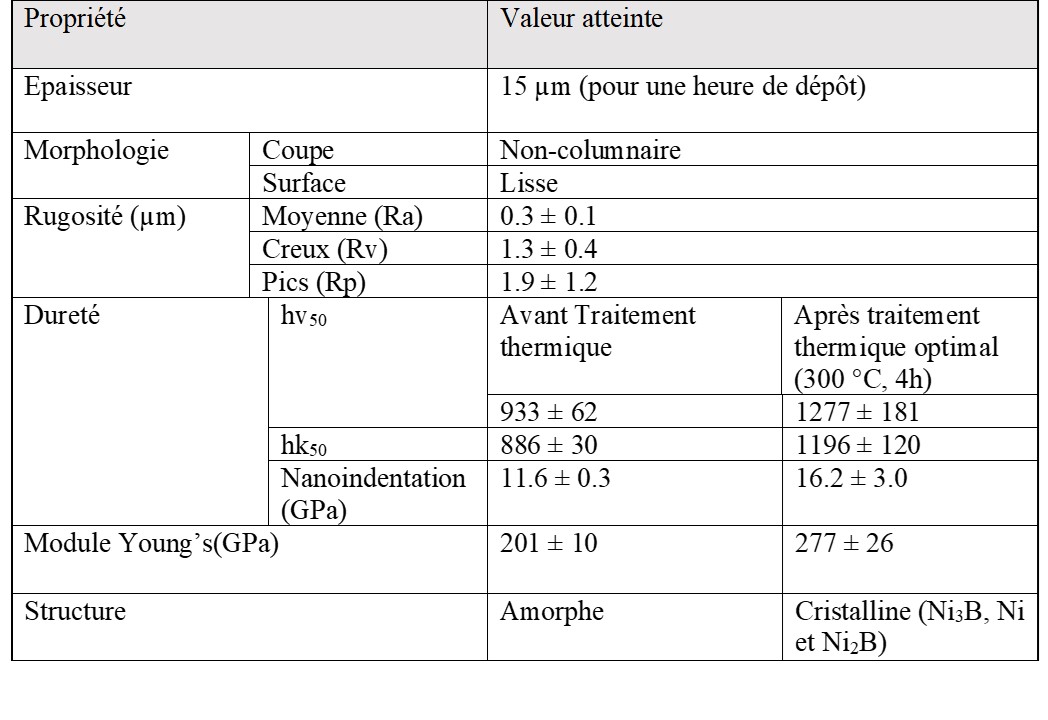
PERFORMANCES
Le
nouveau dépôt présente une meilleure résistance à la corrosion par rapport au revêtement
nickel-bore conventionnel. La première trace de corrosion est observée après 2
jours d’exposition au brouillard salin neutre, contre 1 jour pour les dépôts
conventionnels. Après dix jours d’exposition, la surface corrodée représente
seulement 7.2 % de la surface exposée. Le potentiel de corrosion de nouveau revêtement
est plus élevé que celui du conventionnel revêtement de nickel-bore.
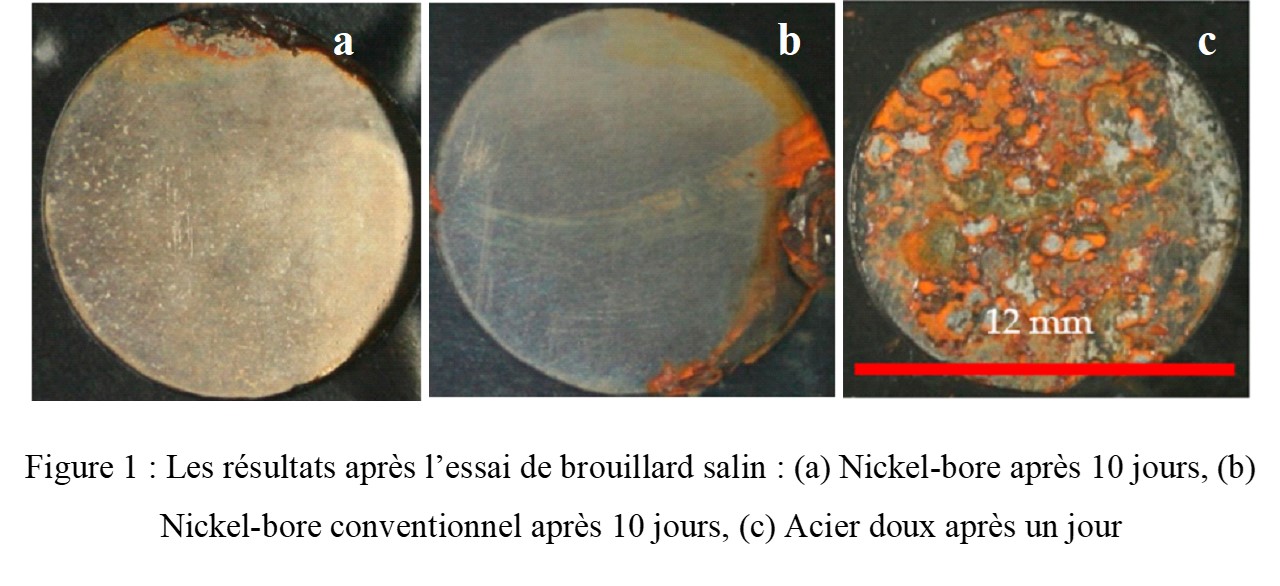
L’indice
d’usure Taber (TWI) du revêtement est 7.3, soit du même niveau que celui du
revêtement de nickel-bore conventionnel (6.2) et que le chrome dur. Le
coefficient de friction du revêtement est 0.47.
MISE EN OEUVRE
La technique de revêtement chimique est mise en œuvre en voie liquide, par immersion dans une solution aqueuse dont le pH est alcalin. La température du processus est 95 °C. et la solution est agitée mécaniquement. L’épaisseur du revêtement dépend de la durée d’immersion.
Les substrats sont traités avant d’être immergés : ils subissent un polissage ou un sablage (destiné à obtenir un état de surface reproductible et une rugosité contrôlée), un dégraissage et une activation. Ces prétraitements sont indispensables pour obtenir un revêtement épais, peu rugueux et présentant une adhérence adéquate sur le substrat.
Un post-traitement est également appliqué dans de nombreux cas. Il s’agit d’un traitement thermique qui permet d’améliorer les propriétés mécaniques et tribologiques du revêtement. Il n’est toutefois pas utilisé de manière systématique.
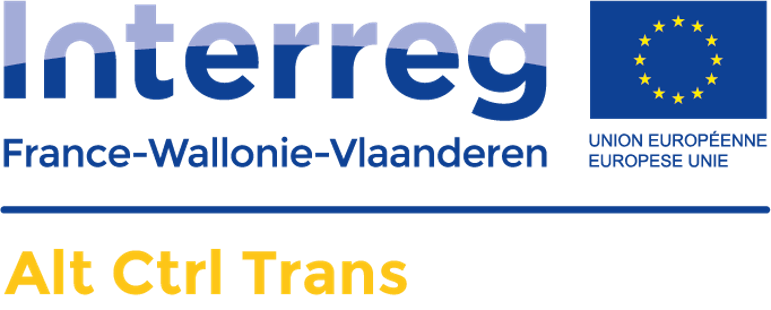